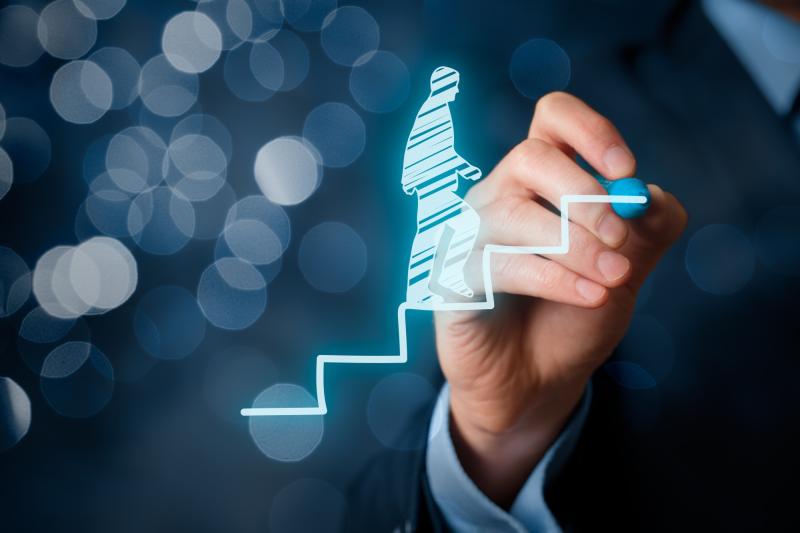
Imagine we're embarking on a time machine journey through the evolution of industry and the transformation of workplaces at large - from factories to banks and beyond. Each stop on our journey is more advanced and thrilling than the last. Buckle up; it's going to be quite the adventure!
Firstly, let us unpack the origins and evolution of these futuristic-sounding terms.
The Genesis of Industry 4.0
The term "Industry 4.0" was introduced in 2011 at the Hannover Fair in Germany, originating from a project within the German government's high-tech strategy, which promoted the computerisation of manufacturing. The "4.0" signifies the fourth industrial revolution. Here's a quick time travel through the Industrial revolutions to see how we got here:
- Industry 1.0 was the era of mechanisation. Think steam engines and waterpower, which kicked off in the late 18th century.
- Industry 2.0 moved us into mass production. Thanks to the introduction of electricity, we could produce goods like never before in the early 20th century.
- Industry 3.0 brought in the digital revolution. Computers started to take the stage, automating production in ways that seemed like science fiction to the steam-powered pioneers.
- Industry 4.0 is the current era in which we're making things smart. It's about blurring the lines between physical and digital with the help of the Internet of Things (IoT), artificial intelligence (AI), robotics, and more. It's not just automation but "smart automation."
And then came Industry 5.0
While we're still navigating the waters of Industry 4.0, forward-thinkers have already started talking about Industry 5.0. Unlike its predecessor, Industry 5.0 isn't about technology for technology's sake. It brings the human touch back into the technological landscape. It's about collaborating with machines to enhance creativity, flexibility, and personalisation. Industry 5.0 aims to make the industrial process more humane and sustainable, focusing on customisations and collaborating with robots rather than being replaced by them.
Why These Terms Matter
The progression from Industry 4.0 to Industry 5.0 represents more than just technological advancements; it signifies a shift in how we think about work, production, and innovation. Industry 4.0 emphasises making machines smarter, but Industry 5.0 reminds us of the value of human intuition, creativity, and decision-making.
The evolution from 4.0 to 5.0 reflects a broader societal shift towards valuing efficiency and ethical considerations, such as sustainability, worker well-being, and social equity. It acknowledges that while machines can make work easier and more efficient, the human aspects of empathy, ethics, and creativity are irreplaceable and should be integrated into technological advancements.
Industry 4.0 and 5.0 aren't just buzzwords; they're markers of our journey through the technological and societal landscapes. They remind us that as we advance, we must balance technology's capabilities with society's values and needs. So, as we stride into the future, let's remember it's not just about building smarter machines but about creating a smarter, more humane world. I suspect the more we use these machines, the more time we need to spend in nature, but that's another entirely different topic!
Welcome to Industry 4.0: The Era of Smart Everything
First up, Industry 4.0. Picture this: if Industry 4.0 transforms a factory into a smart factory, then it turns a bank into a smart bank and a retail store into a smart store. Much like how smart devices in your home communicate to make life easier, Industry 4.0 creates the potential to integrate AI, machine learning, and big data into various sectors, streamlining operations, enhancing customer experience, and making decisions smarter and faster. It's about connectivity and automation everywhere, not just on the production floor but in how we provide and consume services, from personalised banking advice powered by AI to on-demand retail experiences that know your preferences better than you do.
The Broad Impact of Industry 4.0
Stepping into Industry 4.0 could feel like moving into a smart home. The potential is massive for businesses, whether making cars or processing loan applications. Efficiency, cost savings, and hyper-personalised services are just the beginning. For employees, it means adapting to work alongside AI, learning new skills, and embracing a workplace where some of the colleagues are algorithms. It might sound scary, but remember, each industrial revolution has created different jobs and opportunities.
Navigating Change Beyond Manufacturing, that doesn't change!
Managing change in this new era means that everyone understands the benefits of these smart systems, whether on the factory floor or at the bank's front desk. It's like introducing your family to a new smart home gadget; success depends on showing how it makes life better and being honest about the changes. Clear communication, training, and inclusion are key, ensuring everyone feels part of a future and even helping design it.
Fast Forward to Industry 5.0: Human-Machine Harmony
Next, we journey to Industry 5.0, where the focus shifts back to the human element, emphasising collaboration between humans and machines across all sectors. Imagine a bank where AI helps tailor financial advice to each customer's unique life situation or a retail experience that combines the efficiency of automation with the personal touch of human service. It's a partnership dance where technology enhances human creativity and decision-making, aiming for outcomes that are efficient but also ethically sound and personally meaningful.
The transition from Industry 4.0 to Industry 5.0 has additional implications for organisational change. Leaders and managers must adapt to the new opportunities and challenges posed by the emerging technologies and cultivate a culture of innovation, learning and agility. The impacts of Industry 5.0 on organisational change are:
- The need to reskill and upskill the workforce to adapt to the evolving demands and expectations of customers, suppliers and stakeholders.
- Industry 5.0 requires workers to have technical and soft skills like creativity, problem-solving, communication and collaboration.
- The need to revamp the organisational structure and processes to support more flexible, agile and customer-centric operations.
- Collaboration - Industry 5.0 enables more customisation and personalisation of products and services, which requires more collaboration across functions, departments and locations.
- Decentralisation - Industry 5.0 also enables more decentralisation and empowerment of teams and individuals, who can access data and resources anywhere and anytime.
The Wider Impact of Industry 5.0
In Industry 5.0, organisations need to aim to add a layer of empathy to their operations. It's about producing and serving more efficiently, focusing more on sustainability, ethics, and human values. The goal is to utilise technology to enhance the quality of life, not just output.
Embracing Change Across the Spectrum
Adapting to Industry 5.0 across different sectors means creating a culture where technology is seen as an ally in enhancing human work, not a replacement. It involves training people in technical skills and understanding how technology can contribute to meaningful outcomes -for customers, employees, and society.
Conclusion
As our time machine returns to the present, it's clear that the revolutions of Industry 4.0 and 5.0 extend far beyond manufacturing. They're redefining how we work, produce, and interact across all areas of life. Organisations that effectively navigate these changes will see technology as a tool for efficiency and as a partner in building a better future for everyone. Stay curious, embrace change, and remember, the future is not just about what we make or do but how we make and do things better for all.